FESTO –
STANDARDIZE AND
REDUCE COSTS
Find out how FESTO uses Soley to quickly and systematically identify unnecessary redundancy in the product portfolio, thus opening up potential savings in the millions.
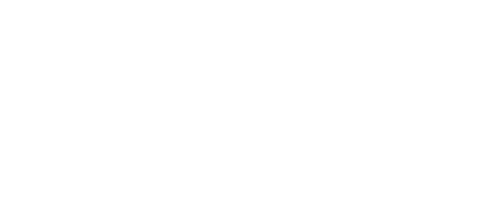
STANDARDIZATION - A SUCCESS STORY
Festo AG & Co. KG uses numerous different cables in its products. When developing new products, it is not always possible to clarify whether a cable used can be replaced by one already in use that meets similar requirements, given the effort involved in a manual investigation. This results in unnecessary cable variants...
"By automating time-consuming manual analyses, we have already been able to systematically reduce unnecessary variety in a short time. This enables us to achieve significant savings in purchasing and reduction of complexity costs. [...] The use of Soley Studio was already worthwhile with the first analysis."
Andreas Kisch, Advanced Product Development
Festo AG & Co.KG